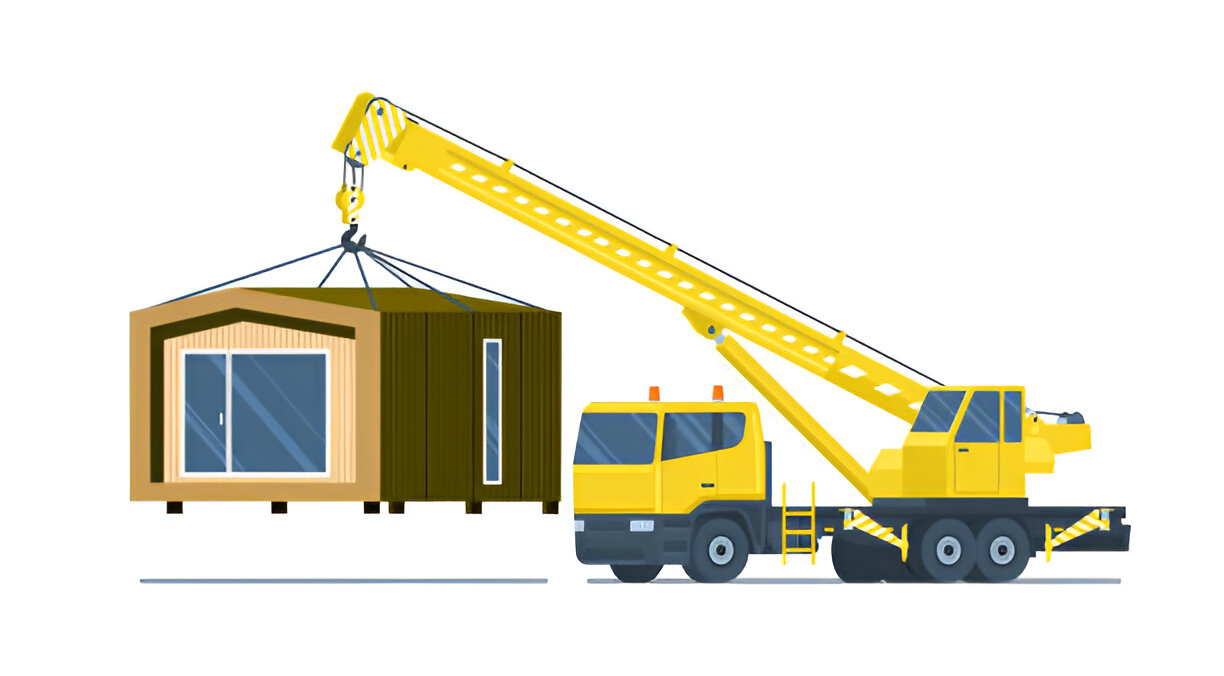
Efficient crane operation is critical for industries such as construction, manufacturing, and shipping. An optimized crane facility can lead to significant improvements in productivity, safety, and cost-effectiveness. This article explores strategies and best practices to enhance the efficiency of your crane facility, covering everything from equipment selection and maintenance to operational protocols and employee training.
1. Choosing the Right Equipment
Assessing Operational Needs
The first step in optimizing a crane facility is selecting the right equipment. Consider the specific needs of your operations, including the types of loads, lifting heights, and the frequency of use. Different cranes, such as tower cranes, mobile cranes, and overhead cranes, offer unique advantages. Matching the right crane to your operational requirements is crucial for efficiency.
Technological Advancements
Incorporate modern technology into your equipment selection. Features such as automated controls, advanced safety systems, and real-time monitoring can significantly enhance performance and safety. Investing in cranes with the latest technology ensures smoother operations and reduces downtime.
2. Regular Maintenance and Inspections
Scheduled Maintenance
Regular maintenance is essential to keep cranes in optimal working condition. Establish a maintenance schedule based on the manufacturer’s recommendations and the operational intensity of your cranes. Preventive maintenance can prevent unexpected breakdowns and extend the lifespan of your equipment.
Routine Inspections
Conduct routine inspections to identify and address potential issues before they become major problems. Inspections should cover structural components, mechanical systems, and safety features. Implementing a checklist for daily, weekly, and monthly inspections helps maintain consistency and thoroughness.
3. Efficient Facility Layout
Space Utilization
An efficient facility layout minimizes unnecessary movement and maximizes space utilization. Arrange your facility to ensure that cranes can operate without obstructions. Position storage areas, loading zones, and workstations strategically to reduce travel time and increase productivity.
Workflow Optimization
Design workflows to streamline operations. Identify and eliminate bottlenecks in your processes. Use techniques such as value stream mapping to visualize and optimize workflows. Efficient workflows reduce idle time and improve overall facility performance.
4. Enhancing Safety Protocols
Comprehensive Training Programs
Safety is paramount in crane operations. Develop comprehensive training programs for all employees involved in crane operations, including operators, riggers, and maintenance personnel. Training should cover equipment operation, safety procedures, emergency response, and regular safety drills.
Safety Technology
Leverage technology to enhance safety. Implement safety features such as anti-collision systems, load monitoring systems, and emergency stop mechanisms. Use real-time monitoring and data analytics to identify potential safety hazards and take proactive measures.
5. Effective Load Management
Proper Load Assessment
Accurate load assessment is crucial for safe and efficient crane operations. Ensure that loads are correctly calculated, and weight limits are strictly adhered to. Overloading cranes can lead to equipment failure and accidents.
Secure Rigging
Implement secure rigging practices to ensure loads are safely and efficiently handled. Use appropriate rigging equipment and techniques for different types of loads. Regularly inspect rigging equipment for wear and tear and replace it as needed.
6. Leveraging Automation and Remote Operations
Automated Systems
Automation can significantly improve the efficiency of crane facilities. Automated systems can handle repetitive tasks with precision and consistency, reducing human error and increasing productivity. Consider integrating automated cranes and material handling systems into your facility.
Remote Operations
Remote operation technology allows operators to control cranes from a distance, enhancing safety and flexibility. Remote operations can be particularly useful in hazardous environments or for tasks that require precise control. Investing in remote operation capabilities can lead to significant efficiency gains.
7. Data-Driven Decision Making
Real-Time Monitoring
Implement real-time monitoring systems to track crane performance and identify inefficiencies. Use sensors and IoT devices to collect data on crane operations, including load weights, operating times, and movement patterns. Analyzing this data can reveal areas for improvement.
Predictive Maintenance
Use data analytics to predict when maintenance is needed. Predictive maintenance relies on real-time data to identify signs of wear and potential failures before they occur. This proactive approach reduces downtime and maintenance costs.
8. Continuous Improvement Programs
Employee Involvement
Involve employees in continuous improvement programs. Encourage operators and maintenance staff to provide feedback on operational challenges and suggest improvements. Implementing a culture of continuous improvement can lead to innovative solutions and increased efficiency.
Benchmarking and KPIs
Establish key performance indicators (KPIs) to measure the efficiency of your crane facility. Use benchmarking to compare your performance against industry standards and identify areas for improvement. Regularly review KPIs and adjust strategies to achieve better results.
9. Energy Efficiency
Energy-Efficient Equipment
Invest in energy-efficient cranes and components. Energy-efficient equipment reduces operational costs and environmental impact. Look for cranes with features such as regenerative braking, which captures and reuses energy during operations.
Sustainable Practices
Implement sustainable practices to reduce energy consumption. This includes optimizing operating schedules to minimize energy use, maintaining equipment to ensure it operates efficiently, and exploring alternative energy sources such as solar power.
10. Effective Communication and Coordination
Clear Communication Channels
Establish clear communication channels among all team members involved in crane operations. Effective communication ensures that everyone is aware of their roles, responsibilities, and any changes in operational procedures.
Coordination with Other Departments
Coordinate with other departments, such as logistics and maintenance, to ensure smooth operations. Effective coordination can prevent delays and improve overall facility efficiency. Use integrated management systems to streamline communication and coordination.
Conclusion
Optimizing your crane facility for maximum efficiency involves a holistic approach that encompasses equipment selection, maintenance, safety, automation, data analysis, continuous improvement, energy efficiency, and effective communication. By implementing these strategies, you can enhance productivity, reduce costs, and ensure the safety of your operations. Regularly reviewing and updating your practices will help maintain high efficiency and adapt to evolving industry standards.
FAQs
1. How often should crane maintenance be performed?
Crane maintenance should be performed regularly, following the manufacturer’s recommendations and the intensity of use. Typically, a comprehensive maintenance schedule includes daily inspections, monthly checks, and annual servicing by a certified professional.
2. What are the benefits of using automated crane systems?
Automated crane systems can handle repetitive tasks with precision, reducing human error and increasing productivity. They also improve safety by minimizing the need for human intervention in hazardous environments.
3. How can I improve the energy efficiency of my crane facility?
Improving energy efficiency involves investing in energy-efficient cranes, optimizing operating schedules, maintaining equipment for optimal performance, and exploring alternative energy sources like solar power. Implementing sustainable practices can also reduce energy consumption.
4. What is the importance of real-time monitoring in crane operations?
Real-time monitoring provides valuable data on crane performance, allowing for the identification of inefficiencies and potential issues before they become major problems. It supports predictive maintenance, enhances safety, and improves overall operational efficiency.
5. How can continuous improvement programs benefit my crane facility?
Continuous improvement programs encourage employee involvement and feedback, leading to innovative solutions and increased efficiency. By regularly reviewing and refining processes, your facility can adapt to changing conditions and maintain high performance standards.