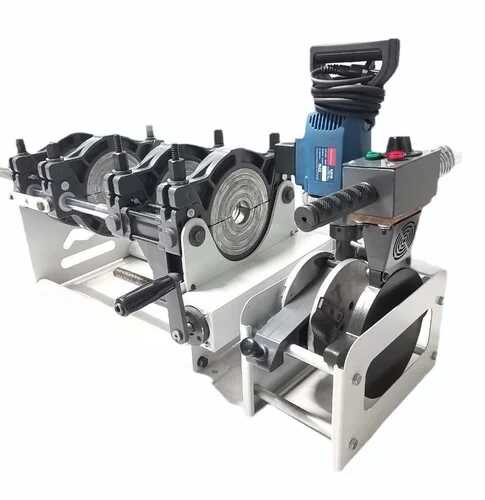
Butt fusion welding is one of the most commonly used methods for joining HDPE (High-Density Polyethylene) pipes in various industries, including water supply, gas distribution, and sewage systems. The process involves heating the ends of the pipes and then pressing them together to form a strong, leak-proof bond. Butt fusion welding machines come in both manual and automatic versions, with manual machines being particularly popular for smaller installations or where budget constraints exist.
In this blog, we’ll explore the role of manual butt fusion welding machines, their advantages, how they work, and why India is home to several leading manufacturers of these essential machines.
What is a Manual Butt Fusion Welding Machine?
A manual butt fusion welding machine is a specialized device designed for joining two pieces of HDPE pipes through the butt fusion process. In this process, the ends of the pipes are heated with a heating plate, and once the material reaches a molten state, the pipe ends are pressed together with a clamping mechanism, creating a permanent bond.
Unlike automatic welding machines, which provide more precise control and require less manual intervention, manual butt fusion machines require the operator to set up the machine, control the heating time, and ensure that the welding pressure is applied correctly. However, they are cost-effective, easy to maintain, and suitable for small to medium-sized projects.
Key Features of Manual Butt Fusion Welding Machines
- Affordable and Cost-Effective
Manual butt fusion machines are generally more affordable compared to their automatic counterparts. This makes them an attractive option for small-scale projects, contractors, and industries with limited budgets. - Compact and Portable
These machines are often compact, lightweight, and portable, making them ideal for field applications or areas with limited space. They can be easily transported to different work sites, making them versatile for various kinds of installations. - Simplicity of Operation
While automatic machines require specialized training, manual butt fusion machines are typically easier to operate. Basic skills in heating, pressure control, and timing are sufficient to complete the fusion process successfully. - Durability and Longevity
Built to withstand the stresses of welding HDPE pipes, manual butt fusion welding machines are designed to be durable, ensuring a long service life even with regular use in challenging environments. - Manual Control for Precision
Manual machines allow operators to adjust the heating time and fusion pressure according to the specific requirements of the pipes being welded, offering a level of flexibility that automatic machines might not provide.
How Manual Butt Fusion Welding Machines Work
- Setup: The pipe ends are first secured in the clamping jaws of the welding machine. The operator ensures that both ends of the pipe are aligned properly.
- Heating: A heated plate is inserted between the two pipe ends. The operator activates the machine, and the plate heats the ends of the pipes to the desired temperature (usually between 200°C and 230°C, depending on the material).
- Fusion: Once the pipe ends have been heated, the operator removes the heated plate and brings the ends of the pipes together under a specific pressure. This ensures the melted surfaces of the pipes fuse together to form a solid joint.
- Cooling: After the fusion, the pipe ends are allowed to cool under pressure to ensure the joint solidifies and forms a strong, permanent bond.
- Inspection: After the cooling period, the joint is inspected for quality and integrity. In some cases, the welded joint is tested for pressure resistance or visual checks are made to ensure there are no gaps or leaks.
Benefits of Using Manual Butt Fusion Welding Machines
- Flexibility in Field Applications: Manual machines are ideal for fieldwork where mobility is crucial. They can be used in remote areas, construction sites, or emergency repair situations where larger, automated machines might be impractical.
- Lower Initial Investment: For small-scale businesses or contractors just starting out, manual butt fusion machines offer an affordable solution without compromising on quality.
- Ease of Maintenance: Manual machines generally have fewer moving parts compared to automatic models, making them easier to maintain and repair.
- Perfect for Small to Medium-Diameter Pipes: These machines are well-suited for joining small to medium-sized HDPE pipes, making them perfect for residential or small infrastructure projects.
Leading Manual Butt Fusion Welding Machine Manufacturers in India
India is home to several reputable manufacturers of manual butt fusion welding machines that offer high-quality, durable machines for diverse applications. Some of the top manufacturers include:
1. Fusion Engineering
Fusion Engineering is a leading manufacturer and supplier of butt fusion welding machines in India. They offer a range of manual butt fusion machines that are known for their reliability, precision, and cost-effectiveness. Their machines are widely used in industries like water, gas, and sewage.
2. Bergman Industrial Group
Bergman is another prominent name in the field of HDPE pipe jointing solutions. Their manual butt fusion welding machines are designed for maximum efficiency and ease of use. With a focus on high-quality materials and engineering, Bergman ensures that their machines deliver excellent performance even in challenging environments.
3. Plasson India
Plasson is a globally recognized brand that offers manual butt fusion welding machines in India. Known for their innovative technology, Plasson provides durable and user-friendly machines that can be used for a variety of pipe diameters and applications. Their equipment is ideal for both field and workshop use.
4. Ritmo India
Ritmo, a global leader in the manufacture of welding equipment, offers a range of manual and automatic butt fusion machines. Their machines are known for being easy to use and highly efficient, making them a popular choice among contractors and small businesses.
5. Technofusion India
Technofusion India specializes in providing high-quality butt fusion welding equipment. Their manual welding machines are designed to be portable, easy to operate, and built for long-term use in the field.
Key Considerations When Choosing a Manual Butt Fusion Welding Machine
When selecting a manual butt fusion welding machine for your project, there are several factors to consider:
- Pipe Size Range: Ensure the machine can handle the pipe diameters you plan to work with. Different machines are designed for various pipe sizes, from small-diameter pipes to larger pipes used in industrial installations.
- Portability: For fieldwork or projects that require flexibility, choose a machine that is lightweight and easy to transport.
- Ease of Use: Consider the skill level required to operate the machine. Manual butt fusion machines are generally easy to use, but some models offer additional features like adjustable pressure gauges or digital timers to improve precision.
- Durability: Look for machines made from high-quality materials that can withstand tough working conditions, whether you’re working in a workshop or in the field.
- After-Sales Support: Choose a manufacturer that offers strong after-sales support, including training, technical assistance, and maintenance services, to ensure the longevity and optimal performance of your machine.
Conclusion
Manual butt fusion welding machines continue to be an essential tool for joining HDPE pipes in various industries. They are reliable, cost-effective, and provide a level of flexibility that makes them suitable for a wide range of applications. In India, several manufacturers offer high-quality manual butt fusion welding machines designed for durability, ease of use, and efficiency.
Whether you are a contractor working on small infrastructure projects or a company involved in large-scale pipe installations, choosing the right manual butt fusion welding machine can ensure the longevity and reliability of your pipelines. Investing in a quality machine will not only save you time and money but also improve the overall performance of your pipe jointing processes.