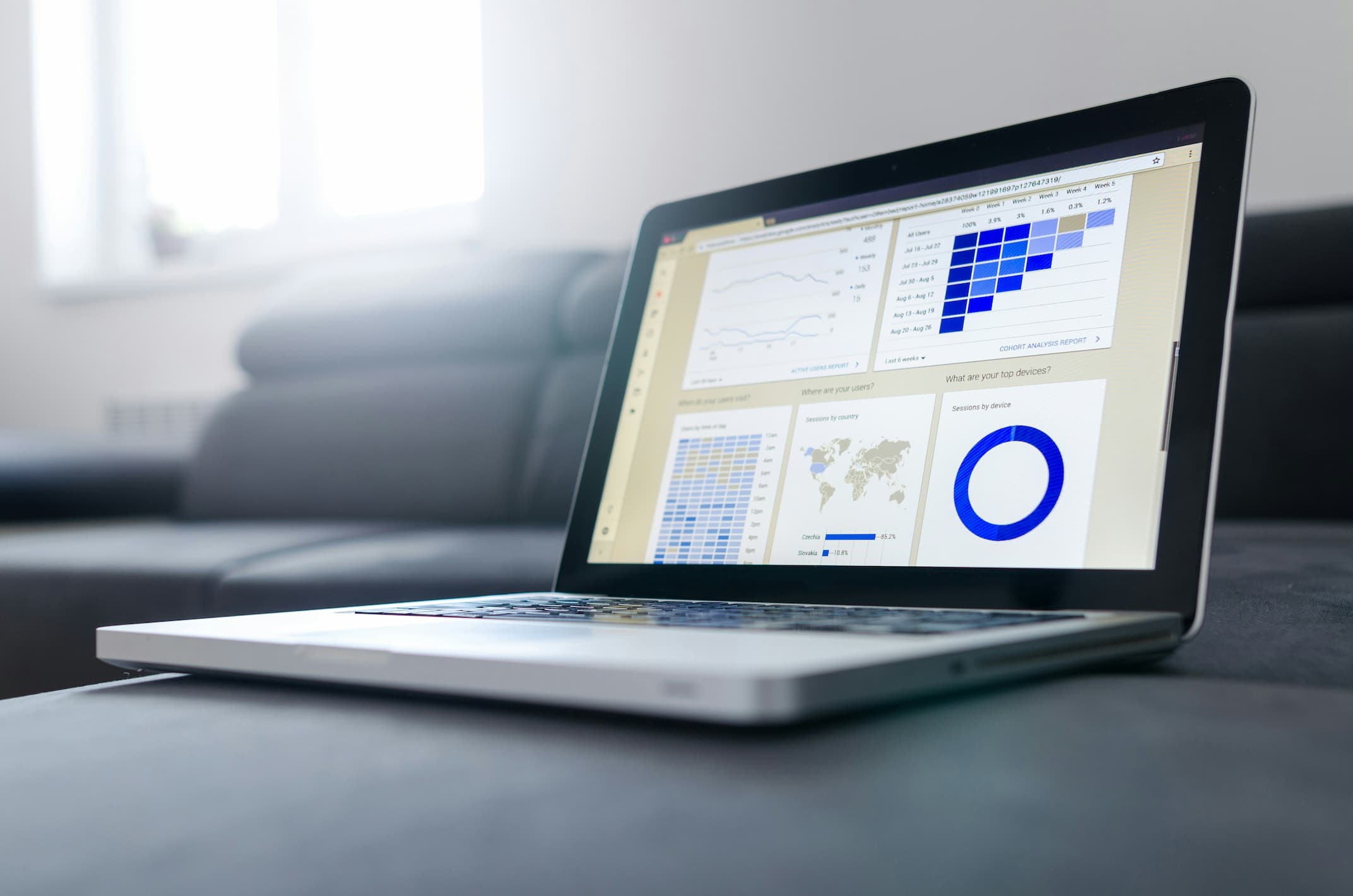
Cross-docking strategies can revolutionize your inventory management. By minimizing storage time and streamlining the flow of goods, cross-docking enhances efficiency and reduces costs.
This approach is gaining popularity among businesses seeking to optimize their supply chain operations. Let’s explore seven key strategies to enhance your cross-docking operations.
What is Cross-Docking?
Cross-docking is a logistics strategy that optimizes the flow of goods from inbound to outbound shipments with minimal storage time. This process benefits from transaction processing and management to accurately track product movement and associated costs. By implementing cross-docking, businesses can significantly reduce inventory holding expenses and enhance overall supply chain performance.
How Cross-Docking Works?
Cross-docking begins when inbound trucks arrive at a distribution center. Workers quickly unload the goods and sort them based on their final destinations. This process often involves scanning barcodes or using RFID technology to track items accurately.
Once sorted, the goods are immediately moved to outbound trucks waiting at the opposite side of the facility. This swift transfer minimizes storage time and handling, reducing the risk of damage and speeding up the delivery process. Cross-docking eliminates the need for long-term warehouse storage, cutting costs and improving efficiency.
7 Cross-Docking Strategies for Optimization
Implement these cross-docking strategies to optimize your inventory management. Each strategy offers unique benefits to enhance your operations. Let’s explore how to apply these techniques effectively.
1. Implement Advanced Technology Solutions
Utilize cutting-edge software and hardware to streamline cross-docking operations. Implement warehouse management systems, barcode scanners, and RFID technology. These tools improve accuracy, speed up processes, and provide real-time visibility into inventory movements.
2. Optimize Facility Layout and Design
Design your cross-docking facility for maximum efficiency. Create a layout that minimizes travel distances between inbound and outbound docks. Use conveyor systems and sorting equipment to speed up the transfer of goods and reduce manual handling.
3. Streamline Inbound and Outbound Processes
Develop standardized procedures for receiving and shipping goods. Train staff on efficient unloading, sorting, and loading techniques. Implement scheduling systems to coordinate inbound and outbound shipments, reducing wait times and improving dock utilization.
4. Enhance Supplier Coordination
Work closely with suppliers to improve the flow of goods. Establish clear communication channels and share data on inventory levels and demand forecasts. Implement vendor compliance programs to ensure consistent packaging and labeling, facilitating faster processing at the cross-docking facility.
5. Utilize Real-Time Data and Analytics
Leverage data analytics to optimize cross-docking operations. Use real-time tracking systems to monitor inventory movements and identify bottlenecks. Analyze performance metrics to continuously improve processes and make informed decisions about resource allocation.
6. Train and Empower Your Workforce
Invest in comprehensive training programs for your cross-docking staff. Teach them efficient handling techniques and how to use technology effectively. Empower employees to make decisions and solve problems on the spot, improving overall operational agility.
7. Develop a Flexible Cross-Docking Model
Create a cross-docking system that can adapt to changing business needs. Implement flexible scheduling to handle fluctuations in volume. Develop contingency plans for unexpected disruptions and cross-train staff to handle various roles within the facility.
Benefits of Cross-Docking
Cross-docking offers numerous advantages for businesses looking to optimize their inventory management. Implement these strategies to experience significant improvements in your supply chain operations. Consider the following key benefits:
-
Reduced Storage Costs: Minimize warehouse space requirements and associated expenses.
-
Faster Order Fulfillment: Speed up the delivery process by eliminating storage time.
-
Improved Inventory Turnover: Increase the rate at which goods move through your supply chain.
-
Lower Labor Costs: Reduce the need for picking, packing, and other warehouse activities.
-
Enhanced Product Freshness: Ideal for perishable goods, ensuring quicker delivery to customers.
Challenges of Cross-Docking and How to Overcome Them?
Cross-docking can present several challenges that businesses must address to ensure success. Recognize these potential issues and implement effective solutions to optimize your operations. Consider the following common challenges and their solutions:
- Coordination Complexity: Use advanced scheduling software to manage multiple shipments.
-
Quality Control: Implement quick inspection processes without slowing down operations.
-
Technology Integration: Invest in compatible systems across your supply chain network.
-
Demand Fluctuations: Develop flexible staffing models to handle volume changes.
-
Space Constraints: Design efficient facility layouts to maximize available space.