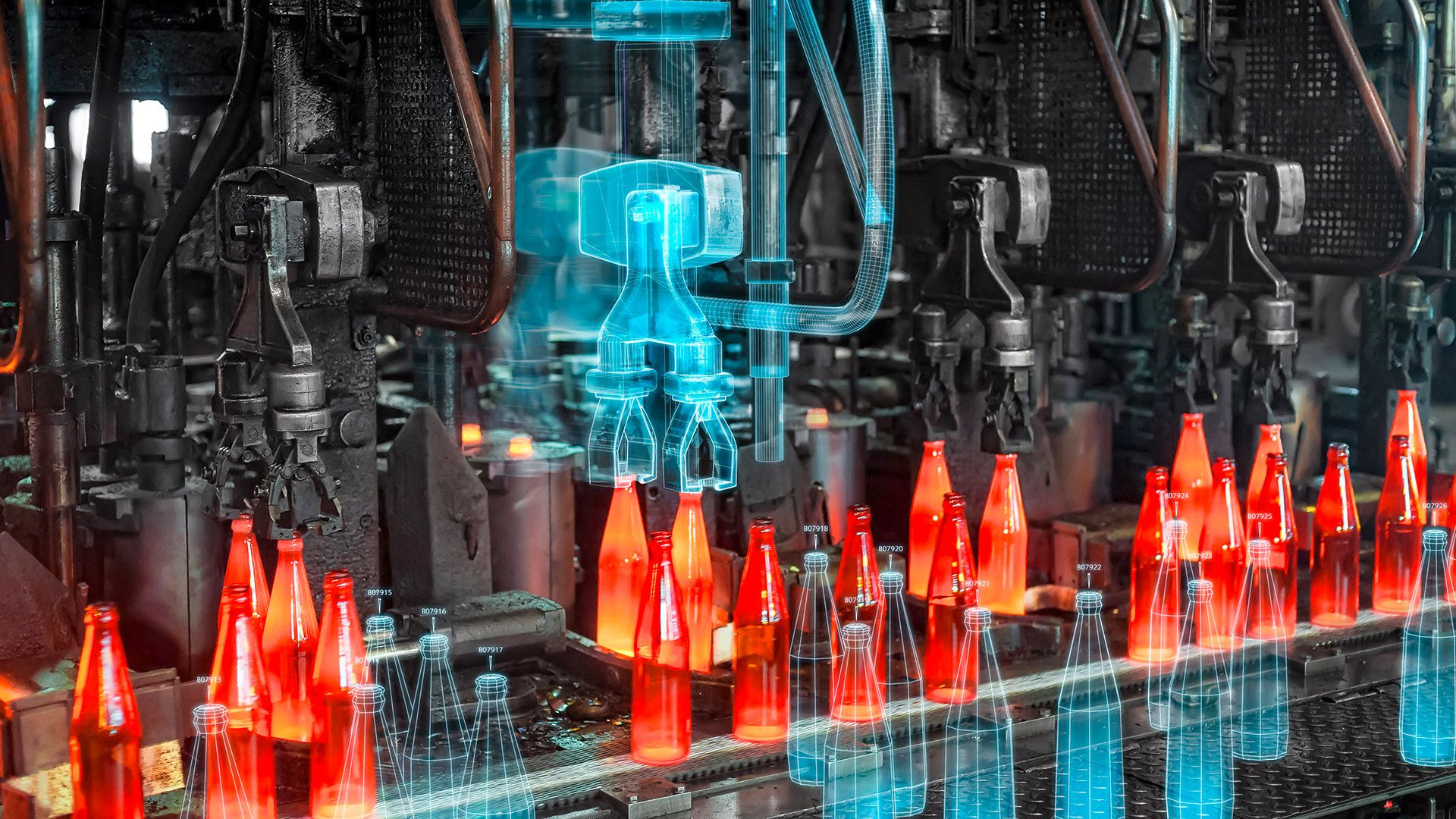
The Future of Glass Forming Machines: How Automation is Transforming the Industry
Glass forming machines play a crucial role in manufacturing various glass products, including bottles, containers, windows, and automotive components. With the rapid advancements in technology, automation is significantly transforming the glass manufacturing industry, enhancing efficiency, precision, and sustainability.
The integration of robotics, artificial intelligence (AI), and smart sensors into glass forming machines is shaping the future of this industry, enabling manufacturers to meet the growing demand for high-quality glass products while reducing costs and environmental impact.
The Evolution of Glass Forming Machines
According to a Glass Forming Machines Market report, the industry is expected to grow significantly in the coming years.
Traditionally, glass forming was a labor-intensive process that relied on manual operations, with workers handling molten glass using rudimentary tools. Over time, mechanical and pneumatic systems improved the process, leading to increased production rates and improved consistency. However, challenges such as human errors, inefficiencies, and material wastage remained prevalent.
With the advent of automation, the industry has undergone a dramatic transformation. Modern glass forming machines are now equipped with advanced robotics and AI-driven control systems that optimize operations, minimize errors, and enhance production capacity. These technological innovations have streamlined the entire glass manufacturing process, from raw material handling to final product inspection.
Automation in Glass Forming: Key Technologies
Automation in glass forming machines is driven by several cutting-edge technologies, including robotics, AI, smart sensors, and the Industrial Internet of Things (IIoT). These technologies work together to improve precision, reduce manual intervention, and enhance productivity.
Robotics and AI Integration
Robotic systems have become an essential component of modern glass forming machines. Robots are used for tasks such as glass handling, shaping, and quality inspection. AI-powered algorithms enable machines to analyze data in real-time, adjusting parameters to optimize production efficiency and ensure product consistency. These AI-driven systems can predict and prevent defects by monitoring temperature fluctuations, pressure variations, and other critical factors during the forming process.
Smart Sensors and IoT Connectivity
Smart sensors play a vital role in automating glass forming machines by providing real-time data on temperature, pressure, and viscosity. These sensors help in maintaining optimal forming conditions, ensuring that each glass product meets stringent quality standards.
The Industrial Internet of Things (IIoT) enables seamless connectivity between machines, allowing manufacturers to monitor and control operations remotely. IIoT-integrated glass forming machines can collect and analyze vast amounts of data, helping operators make informed decisions and improve overall efficiency.
Computerized Numerical Control (CNC) Systems
CNC technology has significantly improved precision in glass forming. CNC-controlled machines allow manufacturers to program complex shapes and intricate designs with minimal errors. This technology is particularly useful in the production of high-end glass products, such as architectural glass panels and decorative glassware.
Benefits of Automation in Glass Forming
The adoption of automation in glass forming machines offers numerous advantages, including increased efficiency, reduced labor costs, improved product quality, and enhanced sustainability.
Increased Production Efficiency
Automation enables continuous production with minimal downtime, resulting in higher output rates. Automated machines can operate 24/7, significantly increasing production capacity compared to manual processes. Additionally, robotic systems perform tasks faster and with greater accuracy, reducing cycle times and increasing overall efficiency.
Enhanced Product Quality and Consistency
One of the major challenges in traditional glass forming is maintaining consistent product quality. Automation eliminates human errors and variations, ensuring uniformity in glass thickness, shape, and surface finish. AI-driven quality control systems detect defects in real-time, reducing waste and improving overall product reliability.
Reduced Labor Costs and Workplace Safety
The glass forming process involves working with high temperatures and molten materials, posing significant safety risks to workers. Automation reduces the need for manual intervention, minimizing exposure to hazardous conditions. This not only enhances worker safety but also reduces labor costs by decreasing the reliance on skilled operators.
Sustainability and Environmental Impact
The glass industry is under increasing pressure to adopt sustainable manufacturing practices. Automated glass forming machines contribute to sustainability by optimizing energy consumption, reducing material waste, and improving resource efficiency. Smart sensors and AI algorithms help monitor and control energy usage, leading to lower carbon emissions and a reduced environmental footprint.
Challenges and Considerations
Despite the numerous benefits, the transition to automated glass forming machines comes with certain challenges. High initial investment costs, technical complexities, and the need for skilled personnel to manage automated systems are some of the key considerations for manufacturers.
High Implementation Costs
Integrating automation into glass forming machines requires significant capital investment. The cost of acquiring robotic systems, AI software, and IIoT infrastructure can be substantial, making it a challenging prospect for small and medium-sized manufacturers. However, the long-term cost savings in labor and operational efficiency often justify the investment.
Technical Expertise and Workforce Training
As automation advances, the demand for skilled technicians and engineers to operate and maintain these sophisticated machines increases. Manufacturers must invest in workforce training programs to equip employees with the necessary skills to manage automated systems effectively.
Integration with Existing Systems
Many glass manufacturers operate legacy machinery that may not be compatible with modern automation technologies. Integrating new automated systems with existing infrastructure can be complex and require customized solutions.
Future Outlook: The Next Phase of Automation in Glass Forming
The future of glass forming machines is poised for further advancements, with emerging technologies set to enhance automation even further. The adoption of digital twin technology, predictive maintenance, and artificial intelligence-driven production planning will revolutionize the industry.
Digital Twin Technology
Digital twin technology creates a virtual replica of a physical glass forming machine, enabling manufacturers to simulate and optimize production processes before implementation. This technology helps in identifying potential issues, improving machine efficiency, and reducing downtime.
Predictive Maintenance with AI
Predictive maintenance powered by AI and IoT sensors will play a crucial role in preventing machine failures. By analyzing real-time data, AI algorithms can predict when a component is likely to fail, allowing manufacturers to perform maintenance before a breakdown occurs. This proactive approach reduces unplanned downtime and extends the lifespan of machinery.
AI-Driven Production Planning
AI will continue to enhance production planning by optimizing resource allocation, scheduling, and material usage. AI-driven systems can analyze market demand, adjust production schedules accordingly, and minimize waste, leading to a more efficient and cost-effective manufacturing process.
Automation is revolutionizing the glass forming industry, offering enhanced efficiency, improved product quality, and greater sustainability. The integration of robotics, AI, smart sensors, and IIoT is driving the industry toward a future of precision manufacturing and reduced operational costs. While challenges such as high implementation costs and technical complexities remain, the long-term benefits far outweigh the drawbacks. As technology continues to evolve, automated glass forming machines will play an even more significant role in shaping the future of glass manufacturing, meeting the growing global demand for high-quality, sustainable glass products.