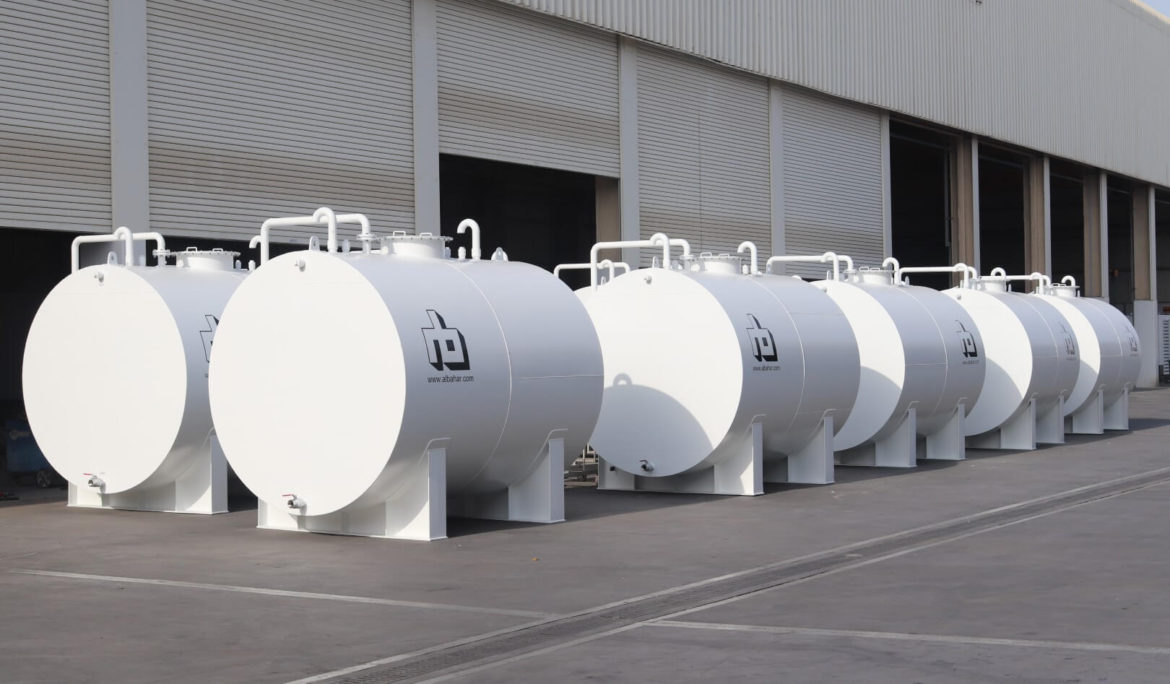
Underground fuel tank installation is a critical process that requires meticulous planning and execution. It plays a vital role in ensuring the safe storage and efficient distribution of fuel. Whether you’re looking to install tanks for commercial or industrial purposes, understanding the intricacies involved can help you make informed decisions. In this guide, we delve into every aspect of underground fuel tank installation, providing you with the knowledge you need to navigate this complex procedure.
Understanding the Basics of Underground Fuel Tanks
Types of Underground Fuel Tanks
Underground fuel tanks come in various shapes, sizes, and materials. The most common types include:
- Steel Tanks: Known for their durability, steel tanks are often coated with corrosion-resistant materials to extend their lifespan.
- Fibreglass Tanks: Lightweight and resistant to corrosion, fibreglass tanks are a popular choice for their long-term reliability.
- Composite Tanks: Combining the benefits of both steel and fibreglass, composite tanks offer enhanced strength and corrosion resistance.
Regulatory Compliance
Compliance with environmental and safety regulations is paramount when installing underground fuel tanks. Various local, state, and federal regulations govern the installation, maintenance, and monitoring of these tanks. It’s crucial to adhere to standards set by agencies like the Environmental Protection Agency (EPA) and other relevant bodies to avoid legal complications and ensure public safety.
Pre-Installation Considerations
Site Assessment and Selection
Choosing the right location for your underground fuel tank is a fundamental step. A thorough site assessment should consider the following:
- Soil Composition: The type of soil can affect the tank’s stability and susceptibility to corrosion.
- Groundwater Levels: High groundwater levels can pose challenges in installation and may require additional precautions.
- Proximity to Buildings and Utilities: The tank’s location should be a safe distance from buildings, utilities, and other structures to minimize risk.
Design and Engineering
Designing the underground fuel tank system involves detailed engineering work. This includes:
- Capacity Planning: Determining the appropriate tank size based on anticipated fuel consumption and storage needs.
- Piping Layout: Designing a piping system that ensures safe and efficient fuel delivery while minimizing the risk of leaks.
- Leak Detection Systems: Installing state-of-the-art leak detection systems to promptly identify any leaks and prevent environmental contamination.
Installation Process
Excavation and Tank Placement
The excavation phase is critical and must be executed with precision. Key steps include:
- Excavation: Digging the hole to the correct depth and width, considering the tank’s dimensions and additional space for backfill materials.
- Tank Bedding: Placing a layer of clean, non-corrosive material, such as sand or pea gravel, at the bottom of the excavation to provide a stable foundation.
- Tank Placement: Carefully lowering the tank into the excavation, ensuring it is level and properly aligned.
Piping and Backfilling
Once the tank is in place, the next steps involve:
- Piping Installation: Connecting the tank to the piping system, ensuring all connections are secure and meet regulatory standards.
- Backfilling: Carefully fill the excavation with suitable materials to protect the tank and piping. This includes compacting the backfill to prevent settling and ensure stability.
Testing and Inspection
Before the tank is operational, rigorous testing and inspection are required:
- Pressure Testing: Conducting pressure tests on the tank and piping to ensure there are no leaks.
- Inspection: A thorough inspection by certified professionals to verify that the installation complies with all safety and regulatory requirements.
Post-Installation Considerations
Monitoring and Maintenance
Regular monitoring and maintenance are essential to ensure the longevity and safety of underground fuel tanks. Key practices include:
- Routine Inspections: Periodic inspections to check for signs of corrosion, leaks, or structural damage.
- Leak Detection: Continuous monitoring using leak detection systems to quickly identify and address any issues.
- Tank Cleaning: Regular cleaning to remove sludge and contaminants that can accumulate over time and affect fuel quality.
Decommissioning and Removal
At the end of their service life, underground fuel tanks must be properly decommissioned and removed. This involves:
- Emptying the Tank: Safely removing any remaining fuel and cleaning the interior.
- Excavation and Removal: Excavating the tank and removing it from the ground, following all safety protocols.
- Site Remediation: Addressing any contamination and restoring the site to its original condition.
Environmental and Safety Considerations
Preventing Contamination
Underground fuel tanks pose potential environmental risks, particularly if leaks occur. Preventative measures include:
- Secondary Containment Systems: Installing barriers or additional containment systems to prevent fuel from escaping into the environment.
- Cathodic Protection: Utilizing cathodic protection systems to prevent corrosion and extend the tank’s lifespan.
Emergency Response Plans
Having a robust emergency response plan is crucial in case of a fuel leak or other incident. This plan should include:
- Immediate Response Actions: Steps to take to contain and mitigate the situation.
- Communication Protocols: Procedures for notifying authorities and stakeholders.
- Cleanup and Remediation: Strategies for cleaning up spills and addressing environmental impacts.
Conclusion
Underground fuel tank installation is a complex process that demands careful planning, precise execution, and ongoing maintenance. By understanding the various aspects involved, from site selection to post-installation monitoring, you can ensure a safe and compliant installation that meets all regulatory requirements. Whether for commercial, industrial, or municipal use, proper installation and management of underground fuel tanks are essential for the safety and protection of both people and the environment.