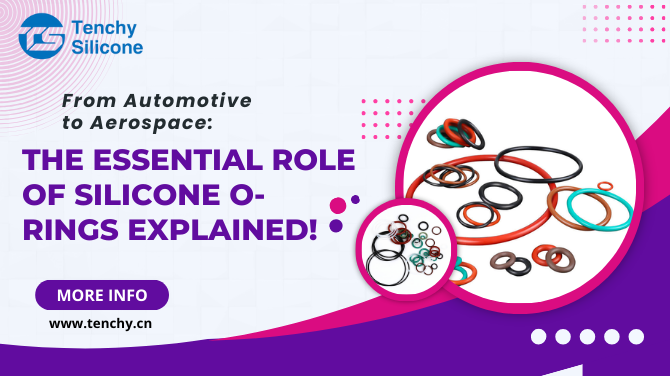
In today’s rapidly evolving industrial landscape, the importance of reliable and efficient sealing solutions cannot be overstated. O rings silicone have emerged as unsung heroes, playing a pivotal role across various sectors, from automotive to aerospace. Their versatility, durability, and effectiveness in providing airtight seals make them indispensable in applications where precision and reliability are paramount.
Understanding the essential role silicone O rings play in machinery and equipment helps us appreciate their contribution to safety, efficiency, and performance. With industries constantly pushing the boundaries of innovation, these seals have adapted and evolved, proving essential for both existing and emerging technologies. Whether it’s in a car’s engine, an aircraft’s hydraulic system, or medical devices, silicone O rings offer the reliability that modern engineering demands.
Understanding O Rings: A Brief Overview
It’s important to understand what O rings are and how they function. An O ring is a circular, doughnut-shaped seal that is placed in a groove to create a barrier between two or more surfaces. This simple yet effective design allows O rings to provide an excellent seal against gases and liquids, preventing leaks and contamination.
O rings can be made from a variety of materials, including rubber, plastic, and metal, but silicone has gained significant traction due to its unique properties. Silicone O rings, in particular, are known for their high temperature resistance, flexibility, and excellent sealing capabilities, making them ideal for a wide range of applications.
The Advantages of Silicone O Rings
When it comes to sealing solutions, silicone O rings offer numerous advantages that set them apart from their counterparts. Here are some key benefits:
- Temperature Resistance: Silicone O rings can withstand extreme temperatures, typically ranging from -60°C to 200°C (-76°F to 392°F). This makes them suitable for both high- and low-temperature applications, ensuring reliable performance even in challenging environments.
- Chemical Resistance: Silicone is inherently resistant to a wide range of chemicals, including oils, solvents, and ozone. This property makes silicone O rings ideal for use in automotive and aerospace applications, where exposure to harsh substances is common.
- Flexibility and Elasticity: Silicone O rings maintain their flexibility and elasticity over time, which helps them create effective seals even after prolonged exposure to pressure and temperature fluctuations. This durability ensures long-lasting performance and reduces the need for frequent replacements.
- Low Compression Set: Silicone O rings exhibit low compression set properties, meaning they retain their shape and sealing ability even after being compressed for extended periods. This characteristic is essential for maintaining effective seals in dynamic applications.
- Versatility: Silicone O rings can be manufactured in various sizes, shapes, and colors, allowing for customization to meet specific requirements. This versatility enables their use in a broad spectrum of industries and applications.
Applications of Silicone O Rings in Various Industries
Silicone O rings find applications in numerous sectors, each benefiting from their unique properties. Here are some of the key industries where these seals play a vital role:
1. Automotive Industry
In the automotive sector, silicone O rings are extensively used in engine components, fuel systems, and HVAC systems. They provide reliable sealing solutions that withstand high temperatures and pressures, ensuring optimal engine performance and fuel efficiency. Their resistance to chemicals and oils further enhances their suitability for various automotive applications.
2. Aerospace Industry
The aerospace industry demands the highest standards of safety and performance. Silicone O rings are utilized in hydraulic systems, fuel systems, and cabin pressure systems to prevent leaks and ensure the integrity of critical components. Their ability to withstand extreme temperatures and environmental conditions makes them essential for aerospace applications, where reliability is paramount.
3. Medical Devices
In the medical field, silicone O rings are used in various devices, including syringes, pumps, and diagnostic equipment. Their biocompatibility and resistance to sterilization processes make them ideal for medical applications, where safety and hygiene are crucial. Silicone O rings help maintain the functionality and accuracy of medical devices, ensuring patient safety.
4. Industrial Equipment
Silicone O rings are widely used in industrial machinery and equipment, providing sealing solutions for pumps, compressors, and valves. Their durability and resistance to wear make them ideal for high-demand applications where failure is not an option. By preventing leaks and contamination, silicone O rings contribute to the overall efficiency and longevity of industrial equipment.
5. Food and Beverage Industry
In the food and beverage sector, silicone O rings are employed in various applications, including packaging, processing, and storage. Their resistance to high temperatures and chemicals ensures the safety and quality of food products. Additionally, silicone is a non-toxic material, making it suitable for contact with food and beverages.
Best Practices for Installing Silicone O Rings
Proper installation of silicone O rings is crucial to ensuring optimal performance and longevity. Here are some best practices to follow:
- Clean the Groove: Before installing the O ring, ensure that the groove is clean and free from debris, dust, or contaminants. This step is essential to achieving a proper seal.
- Lubricate the O Ring: Applying a thin layer of lubricant to the O ring can help ease installation and reduce friction. Be sure to use a lubricant compatible with silicone and the fluids the O ring will encounter.
- Avoid Twisting: When installing the O ring, avoid twisting or stretching it, as this can lead to deformation or damage. Instead, gently press the O ring into the groove to ensure a snug fit.
- Check for Proper Fit: After installation, visually inspect the O ring to ensure it is seated correctly in the groove. This step is essential to prevent leaks and ensure effective sealing
- Regular Maintenance: Periodically check the O rings for signs of wear, damage, or deterioration. Regular maintenance can help identify potential issues early and prevent costly failures.
Silicone O rings play an essential role in a wide range of industries, from automotive to aerospace, thanks to their unique properties and versatility. Understanding the advantages and applications of these seals is crucial for anyone involved in engineering, manufacturing, or maintenance. By choosing silicone O rings for sealing solutions, companies can ensure reliability, safety, and efficiency in their operations.
As industries continue to innovate and push the boundaries of technology, the demand for high-quality silicone O rings will only increase. Investing in these essential components not only enhances product performance but also contributes to the overall success of various applications.
In summary, silicone O rings are more than just seals; they are vital components that ensure the safe and efficient operation of countless systems and devices. Whether you’re in the automotive, aerospace, or medical field, understanding and utilizing O rings silicone can make a significant difference in your product’s performance and longevity.
FAQs
1. What are silicone O rings made of?
Silicone O rings are made from silicone rubber, a versatile material known for its excellent temperature resistance, chemical resistance, and flexibility.
2. What industries commonly use silicone O rings?
Silicone O rings are used in various industries, including automotive, aerospace, medical devices, industrial equipment, and food and beverage.
3. How do I know if I need to replace my silicone O rings?
Signs of wear, such as cracks, tears, or deformation, indicate that your silicone O rings may need replacement. Regular inspections can help identify potential issues early.
4. Can silicone O rings be used in high-temperature applications?
Yes, silicone O rings are designed to withstand extreme temperatures, typically ranging from -60°C to 200°C (-76°F to 392°F), making them suitable for high-temperature applications.
5. What are the best practices for installing silicone O rings?
Best practices for installing silicone O rings include cleaning the groove, lubricating the O ring, avoiding twisting, checking for proper fit, and conducting regular maintenance.